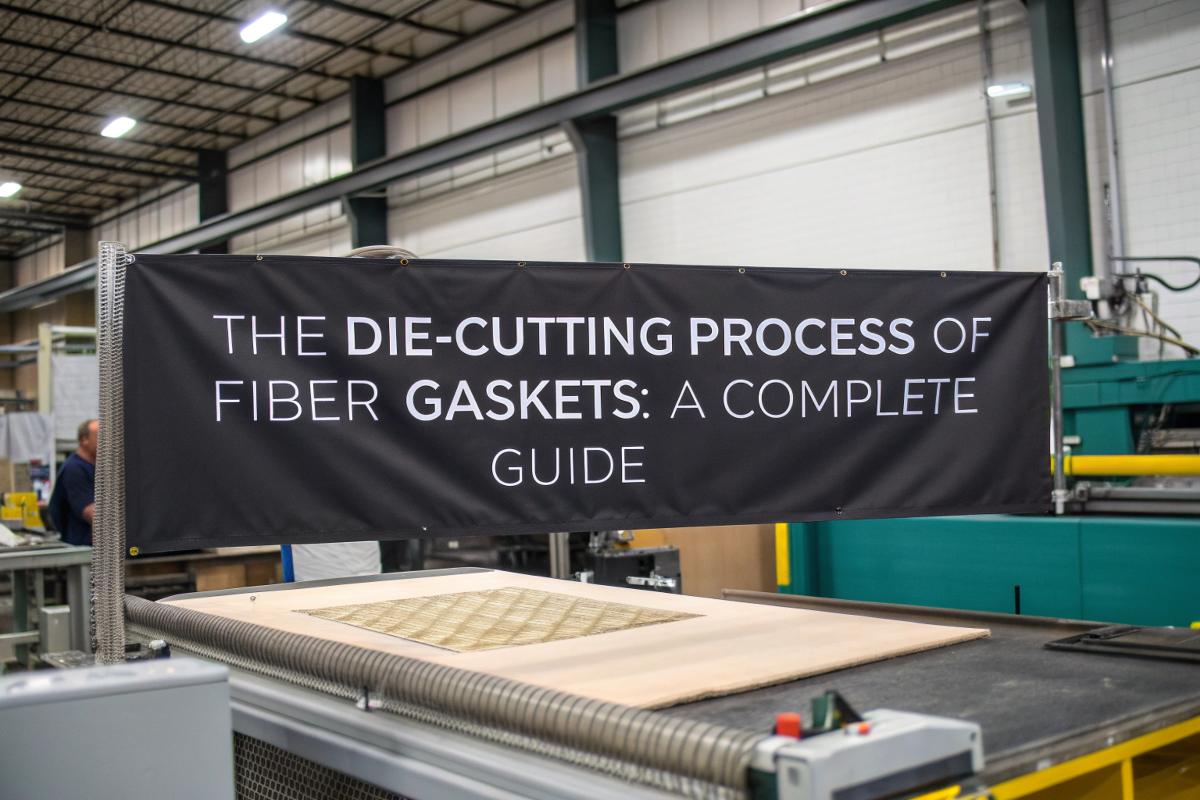
Fiber gaskets play a crucial role in various industries, ensuring reliable sealing under extreme conditions. These gaskets are made from reinforced fibers combined with rubber or resin, providing excellent heat resistance, chemical resistance, and durability. But how exactly are they manufactured?
Today we will take you through the die-cutting process of fiber gaskets, covering material selection, cutting techniques, quality control, and industry applications.
Get ready for a deep dive into Jiepu precision manufacturing!
1. Material Selection: The Foundation of a Great Gasket
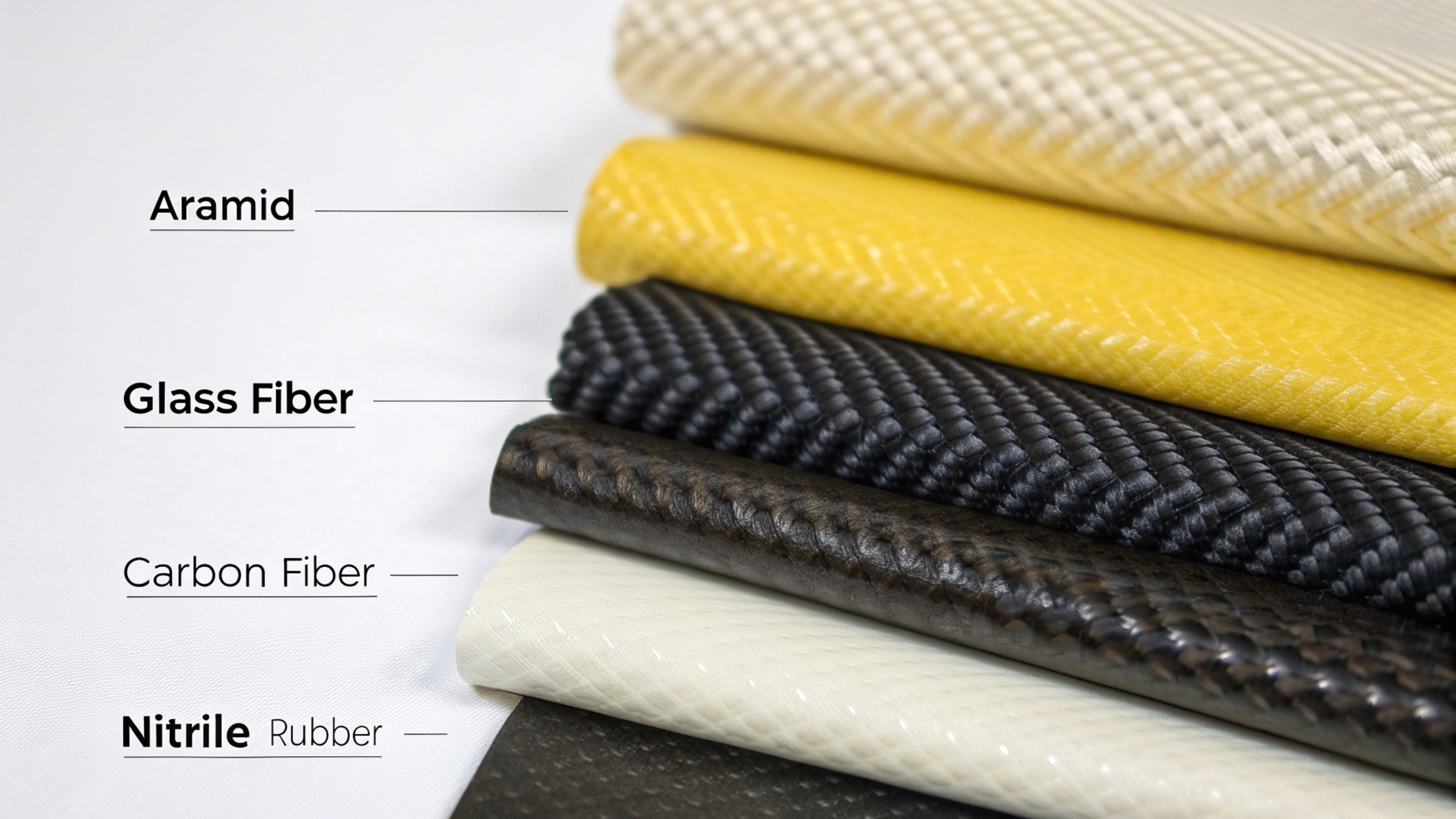
Before the cutting process begins, the choice of materials is essential. Fiber gaskets typically consist of the following:
Material Type | Examples | Key Properties |
---|---|---|
Reinforced Fibers | Aramid (Kevlar), Glass Fiber, Carbon Fiber | High strength, asbestos-free, heat-resistant |
Binders | Nitrile Rubber (NBR), Fluoroelastomer (FKM), Phenolic Resin | Enhances flexibility and sealing capability |
Fillers | Calcium Carbonate, Mica | Improves heat resistance and stability |
Why These Materials?
Non-asbestos alternatives: Safer and environmentally friendly.
Rubber binders: Provide elasticity and sealing efficiency.
Fillers: Help withstand high temperatures and harsh chemicals.
2. Jiepu Die-Cutting Process: From Raw Material to Precision Gaskets
Step 1: Material Pre-Treatment
Before cutting, the raw materials go through several preparatory steps:
Calendering: Fibers and rubber are compressed into uniform sheets.
Pre-curing: Some materials undergo heat treatment to enhance stability.
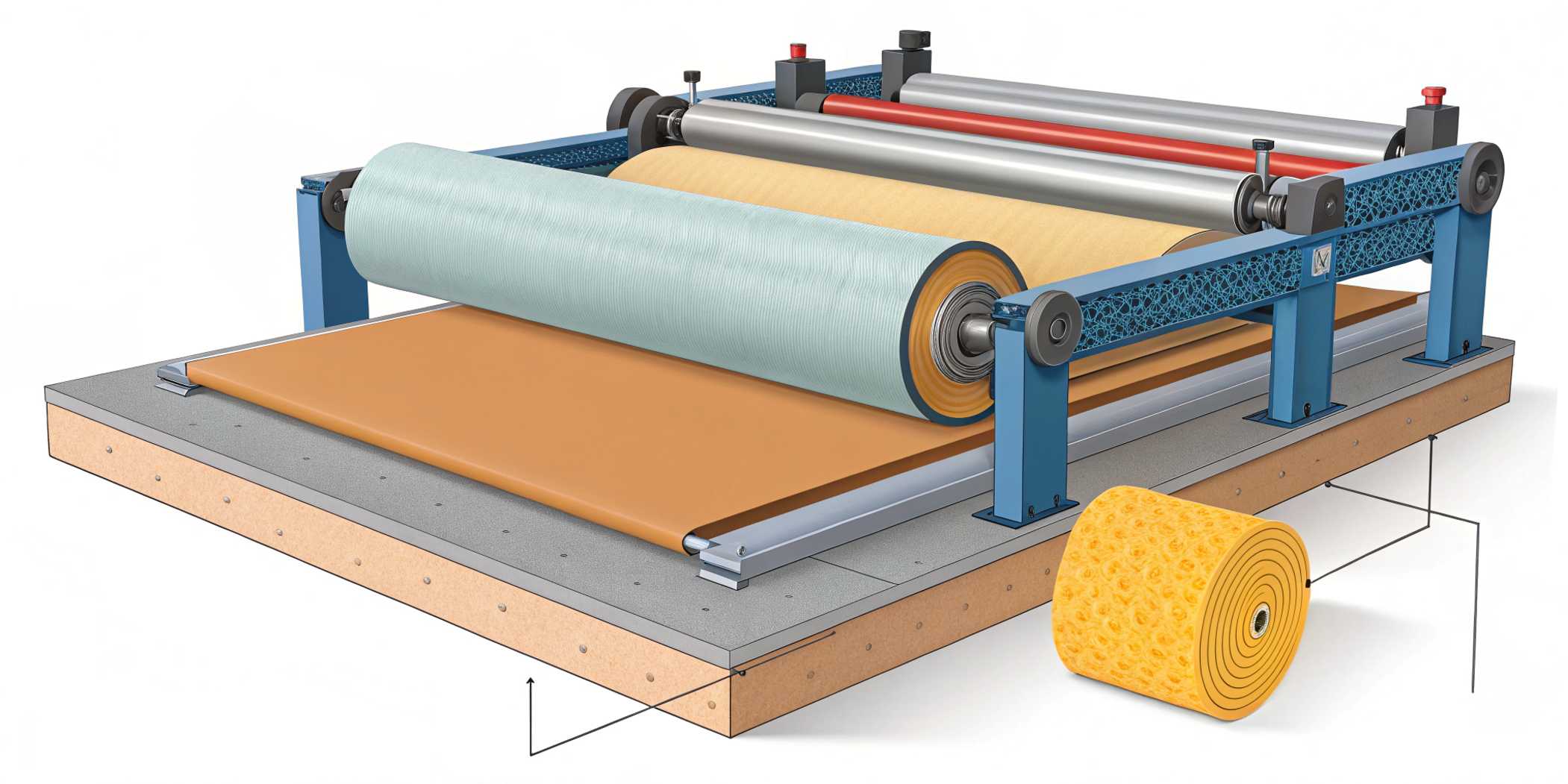
Step 2: Die Design & Tooling
Creating a precise gasket requires carefully engineered dies. The choice of die-cutting technology depends on production needs:
Die Type | Best For | Pros |
Flatbed Die-Cutting | Small batch production | Cost-effective, precise |
Rotary Die-Cutting | High-speed, large volumes | Fast, continuous processing |
Laser Cutting | Complex shapes, no tool wear | Ultra-precise, no need for molds |
🛠️ Pro Tip: The die-cutting blade angle (typically 45°-60°) is carefully adjusted to minimize burrs and ensure smooth edges.
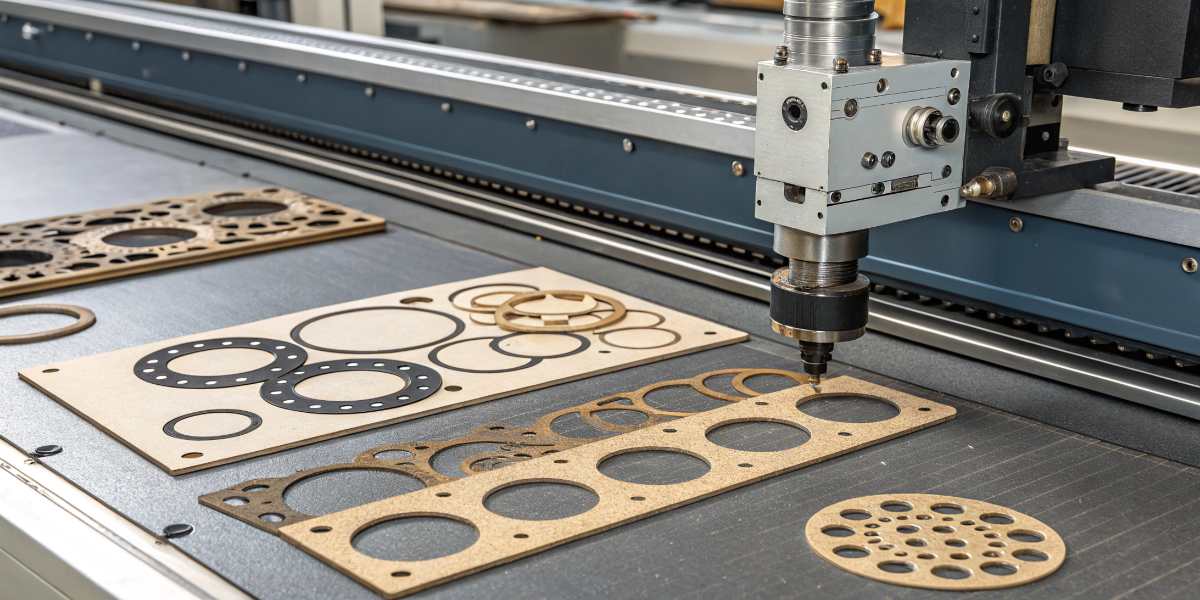
Step 3: Cutting & Processing
Once the material is ready and the die is set, the cutting process begins.
Automatic feeding systems ensure sheet alignment with a precision of ±0.1mm.
Pressure adjustments are made based on gasket thickness (ranging from 0.5mm to 6mm).
Speed control varies: Rotary die-cutting can reach 100 meters per minute, while laser cutting offers slower but unmatched accuracy.
Step 4: Post-Processing for a Perfect Finish
Scrap removal: Vacuum suction or mechanical stripping clears excess material.
Surface coating: PTFE spray improves chemical resistance.
Secondary curing: Some gaskets need additional heat treatment at 150°C-200°C.
🚀 Did You Know? Laser cutting eliminates tool wear, but rotary die-cutting is up to 5x faster!
3. Ensuring Quality: Precision Testing & Inspection
Even the best die-cutting process needs strict quality control to ensure top performance.
Key Quality Control Measures
Dimensional Accuracy: Optical projectors and Coordinate Measuring Machines (CMMs) verify tolerances within ±0.05mm.
Compression & Recovery Testing: Following ASTM F36 standards to assess resilience.
Creep Relaxation Tests: ASTM F38 ensures gaskets maintain sealing pressure over time.
Common Defects & Solutions
Issue | Cause | Solution |
Burrs & Rough Edges | Dull blades or incorrect pressure | Sharpen die-cutting tools, adjust pressure |
Material Warping | High humidity or improper storage | Store at 25°C/50%RH, pre-dry materials |
Sticking to Die | High friction between gasket & mold | Apply Teflon coating to dies, use release paper |
🔎 Quality Fact: Some fiber gaskets require microscopic testing to detect invisible cracks or weak points.
4. Environmental & Safety Considerations
Keeping the Workplace Safe & Clean
Die-cutting fiber gaskets, especially those containing glass fibers, can generate dust.
HEPA filters help remove fine particles from the air.
Automated waste disposal minimizes contamination.
Eco-Friendly Trends
New gasket materials focus on sustainability:
Halogen-free composites reduce environmental impact.
Bio-based fiber gaskets, such as flax fiber-reinforced materials, offer renewable alternatives.
🌍 Future Outlook: Expect more recyclable and biodegradable gasket materials in the coming years!
5. Real-World Applications: Where Fiber Gaskets Matter
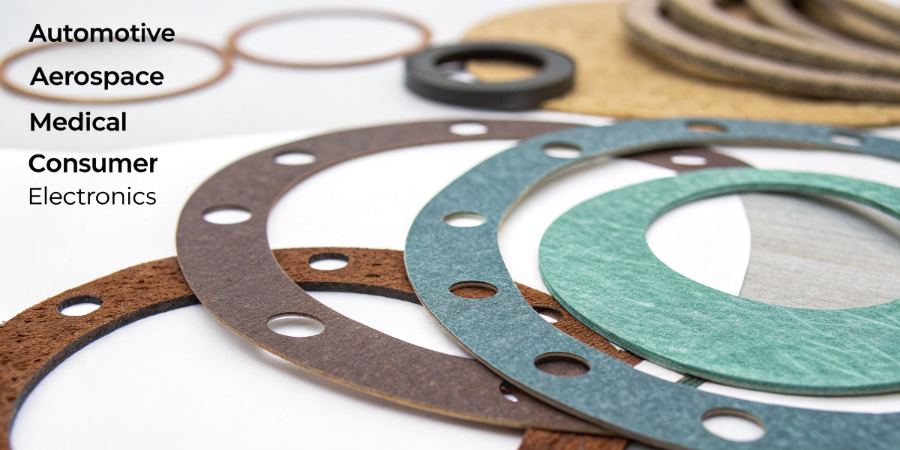
Fiber gaskets are widely used across industries due to their versatile sealing properties. Here are some common applications:
Industry | Application | Key Requirement |
Automotive | Exhaust system gaskets | Heat resistance up to 800°C |
Industrial Machinery | Valve and pump seals | Chemical resistance |
Aerospace | Engine compartment gaskets | Lightweight yet durable |
💡 Case Study: An automotive manufacturer reduced engine leakage failures by 30% after switching to high-performance aramid fiber gaskets.
Die-cutting fiber gaskets is a precise and technical process that demands the right materials, advanced cutting techniques, and strict quality control. Whether for high-temperature automotive applications or chemical-resistant industrial seals, fiber gaskets play a critical role in performance and safety.
🔹 Key Takeaways: ✔ Material selection is crucial—Kevlar, glass fiber, and NBR are top choices.
✔ The right cutting process—flatbed, rotary, or laser—ensures efficiency and accuracy.
✔ Post-processing, including coatings and heat treatment, enhances durability.
✔ Quality control measures prevent defects and guarantee reliability.
✔ Sustainability is shaping the future of gasket materials.
Now that you know how fiber gaskets are die-cut and manufactured, are you ready to choose the right solution for your industry? Let’s create high-performance seals that last! 🚀