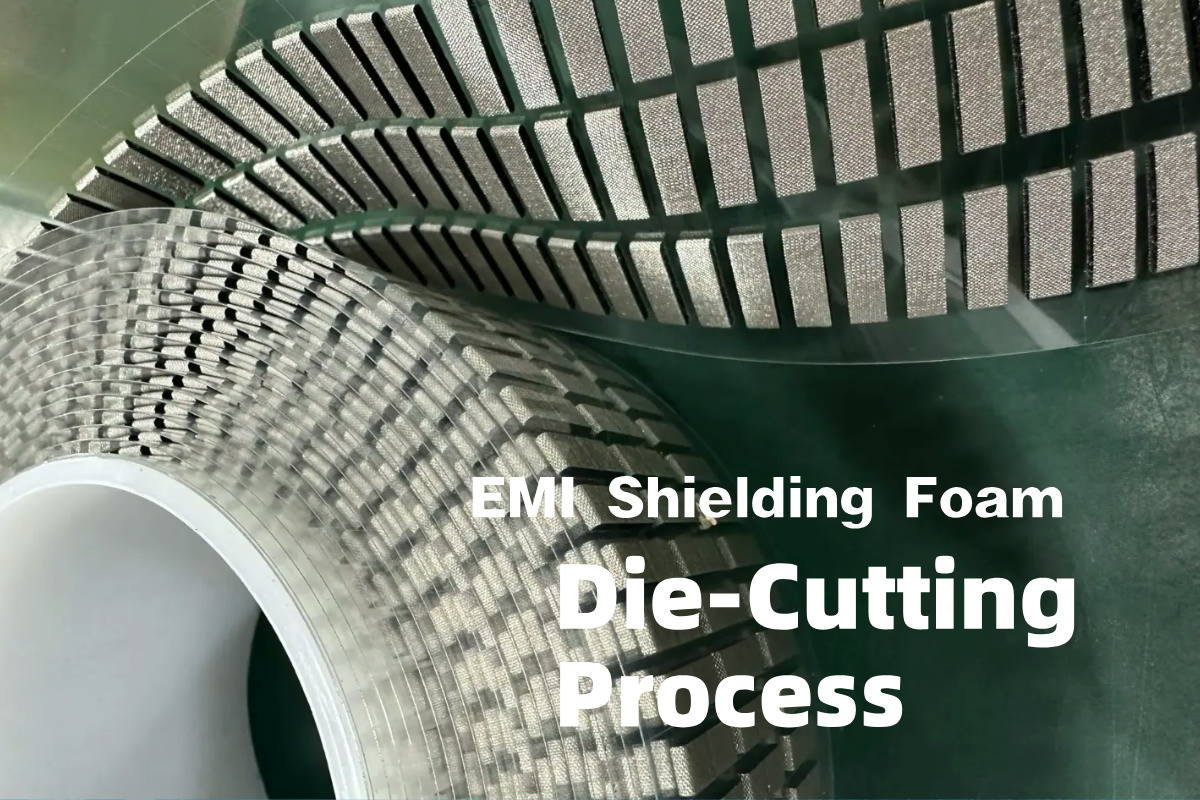
Electromagnetic interference (EMI) is a significant concern in today’s technologically advanced world.
Our devices, from smartphones to sophisticated medical equipment, must operate without disruptive interference.
One of the most effective solutions to this challenge is the use of die-cut EMI shielding foam.
We will show you the intricacies of its processing, applications, and our benefits.
1. Material Selection
The foundation of effective EMI shielding lies in the choice of materials.
Conductive foams are the primary materials used due to their high electrical conductivity and excellent shielding properties.
Common materials include:
Conductive Polyurethane Foam: Known for its elasticity, compressibility, and superior shielding performance.
Fabric-Over-Foam: This involves covering foam with conductive fabric or metal foil to enhance shielding effectiveness.
Other Conductive Foams: Such as carbon-coated foams or foams filled with conductive particles.
2. Die-Cutting Process
Die-cutting is the process of converting raw materials into specific shapes and sizes to fit various applications. The primary methods include:
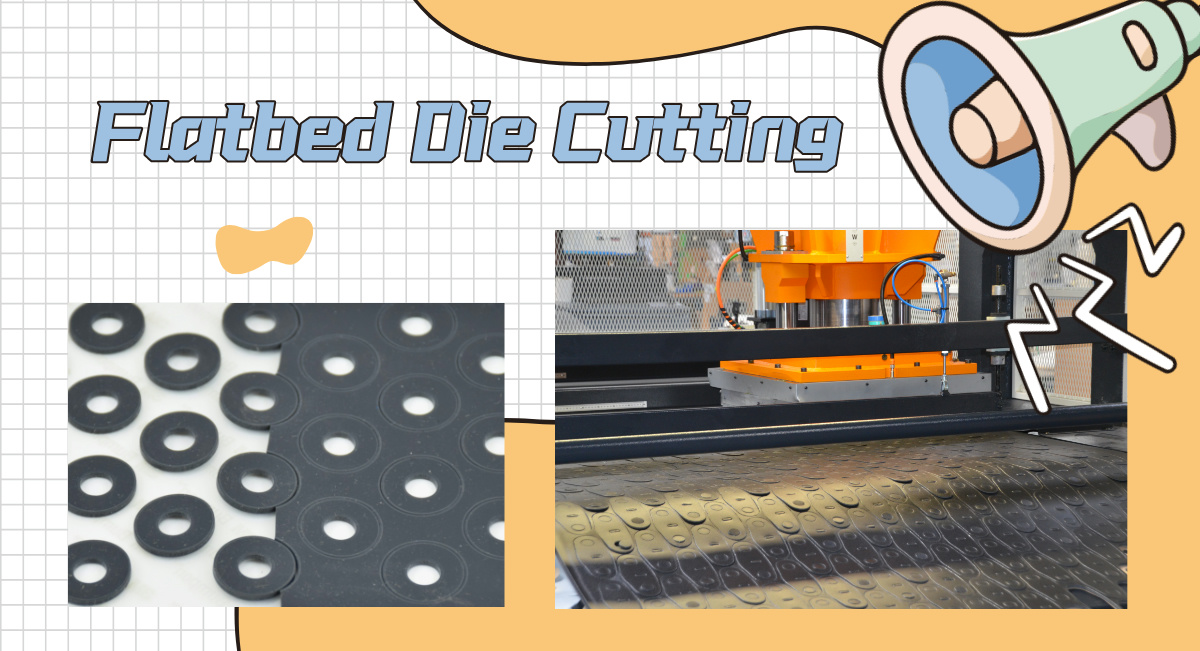
a. Flatbed Die Cutting
Steel Rule Die Preparation: Thin steel strips are shaped into the desired design and mounted onto a base.
Die Installation: The die is secured onto a press machine, facing downward.
Cutting: Material is placed beneath the die, and pressure is applied to cut the material into the desired shape.
Depth Control: Adjustments can be made for full cuts or partial cuts (e.g., “kiss cuts”) to facilitate subsequent processing.
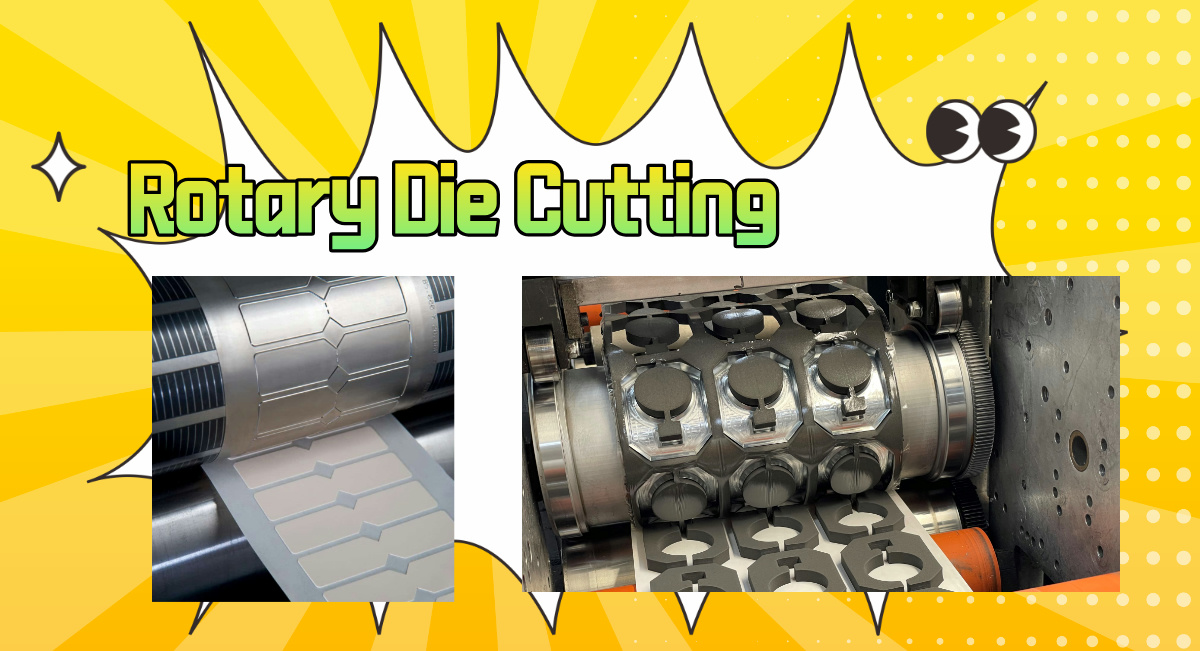
b. Rotary Die Cutting
Equipment Setup: Utilizes cylindrical dies in rotary die-cutting machines, ideal for high-volume production.
Material Feeding: Materials, either in rolls or sheets, are fed into the machine’s processing station.
Cutting and Forming: The rotating die cuts, punches, scores, or trims the material into the specified shapes.
Precision and Waste Management: Accurate gear calibration ensures high precision, minimal waste, and efficient scrap handling.
3. Surface Treatment and Coating
To enhance the shielding effectiveness, surface treatments are often applied:
Conductive Coatings: Applying conductive layers or metallization to the foam’s surface improves conductivity and shielding performance.
Performance Metrics: For instance, fabric-over-foam gaskets can achieve surface resistances below 0.08Ω/□ and shielding effectiveness exceeding 65dB.
4. Adhesion and Assembly
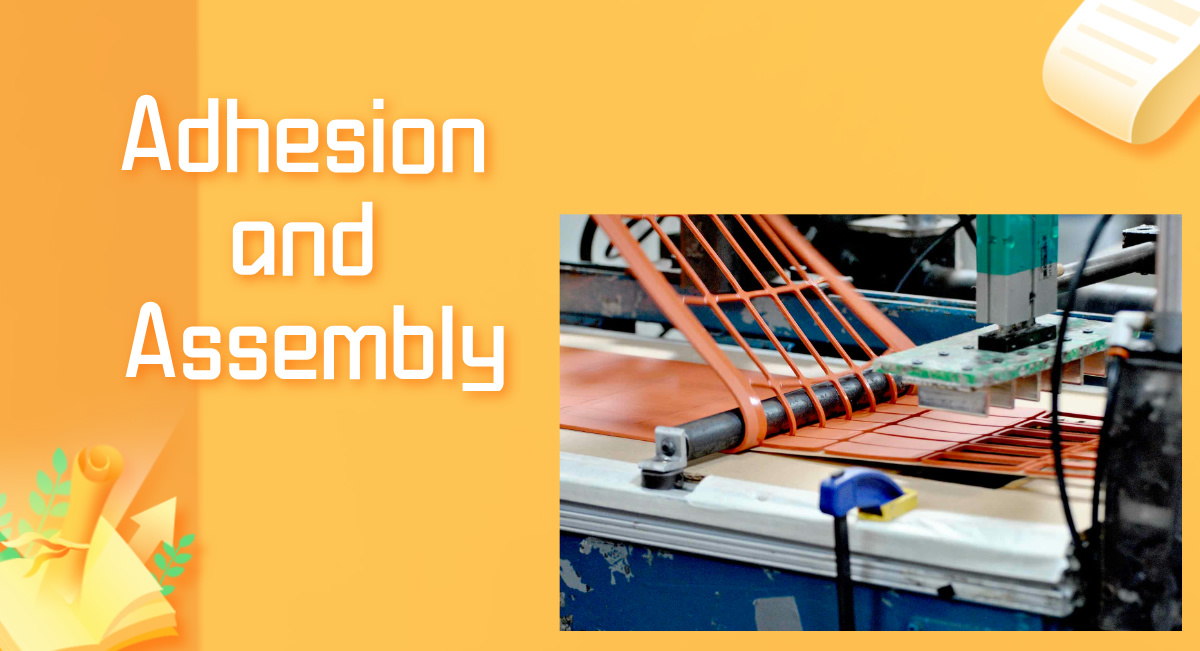
For easy installation, EMI shielding foams are often equipped with adhesive backings:
Double-Sided Tapes: Allow direct attachment to electronic enclosures or internal components.
Adhesive Selection: Must consider the operating environment and compatibility with the substrates.
5. Quality Control and Testing
Post-production, rigorous quality checks are essential:
Dimensional Accuracy: Ensuring the parts meet specified tolerances.
Electrical Conductivity: Verifying the material’s conductive properties.
Shielding Effectiveness: Testing the material’s ability to block or attenuate electromagnetic interference.
Compliance: Ensuring adherence to environmental and safety standards such as RoHS and UL94V-0.
6. Applications
Die-cut EMI shielding foams are integral to various electronic applications:
Electronic Enclosure Sealing: Preventing EMI from entering or exiting device housings.
Touch Sensor Sealing: Serving as electrodes connecting touchscreens to printed circuit boards (PCBs).
High-Frequency Equipment Shielding: Suitable for scenarios requiring high shielding effectiveness.
How to Choose the Right EMI Shielding for Your Needs?
At Jiepu, we don’t just provide die-cut EMI shielding foam—we deliver precision, quality, and reliability. With over 20 years of expertise and state-of-the-art die-cutting technology, we ensure your electronic components are fully protected from electromagnetic interference.
✅ ISO9001, ISO14001, and IATF 16949 certified
✅ Advanced cleanroom facilities for high-precision manufacturing
✅ Custom die-cut solutions tailored to your application needs
✅ High-volume production capacity—up to 3 million parts per day
Looking for high-performance EMI shielding solutions? Contact Jiepu today and get a free quote! 📩