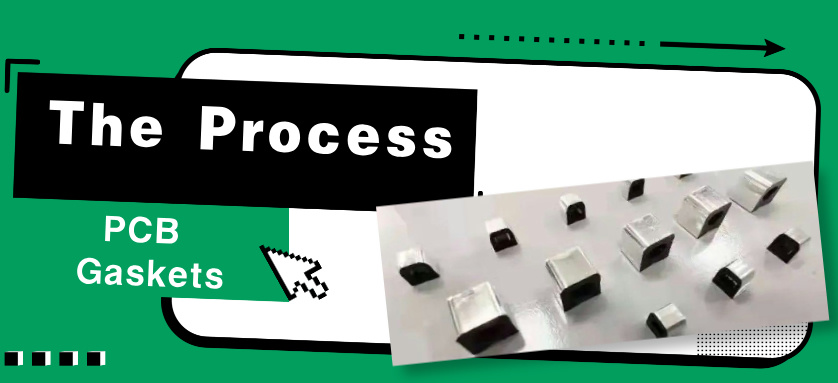
Let’s talk about PCB Shielding Gaskets.
If you’re in the electronics industry, you already know how critical it is to protect circuits from electromagnetic interference (EMI).
These gaskets are the best way to do it.
They’re strong, reliable, and built for success.
Let’s go step by step through how they’re made, and why they matter.
Step 1: The Right Materials – Only the Best
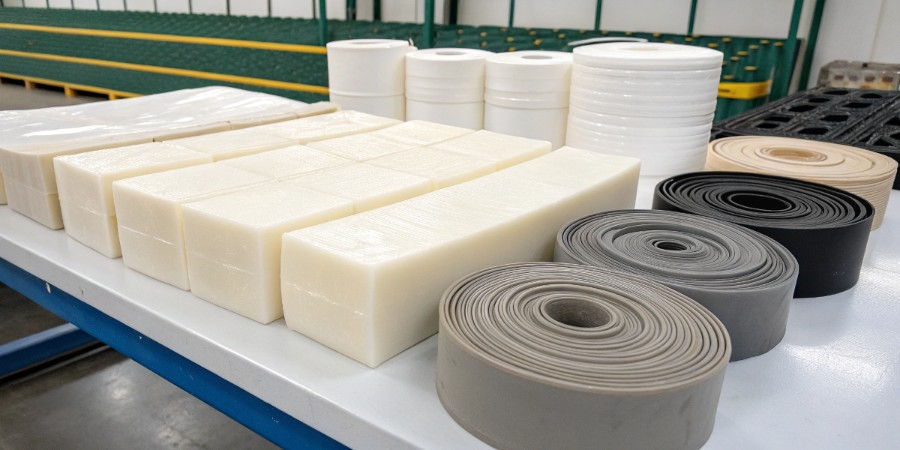
You can’t make a great shielding gasket without great materials.
That’s the key. The main ingredient? Conductive rubber.
We’re talking about high-quality silicone or synthetic rubber, infused with tiny conductive particles—silver-coated copper, nickel-coated graphite, or even silver-coated aluminum.
These materials make the gasket both flexible and conductive, which is exactly what you want.
And it doesn’t stop there. We also need conductive foil—aluminum or copper—for some types of gaskets.
Then, there’s adhesive—sometimes conductive, sometimes not, depending on the design.
Everything is selected for top performance, no exceptions.
Step 2: Creating Conductive Rubber – The Magic Happens Here
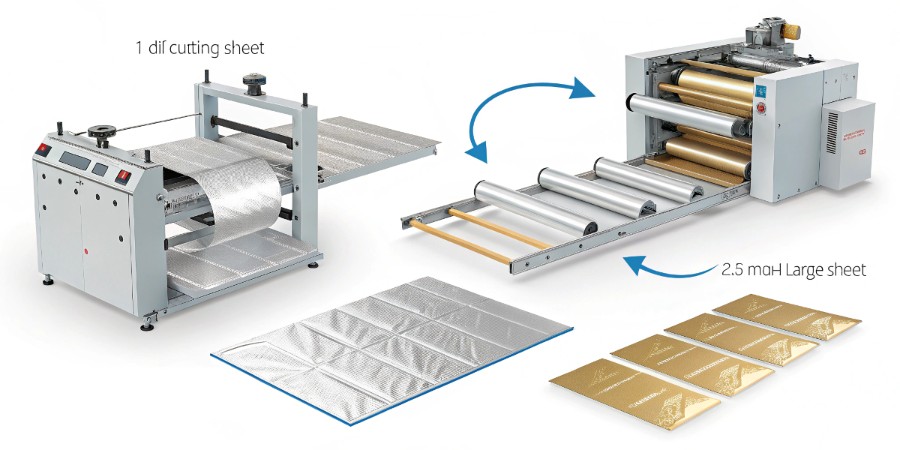
Now, this is where things get really exciting.
We take the rubber base material, mix it thoroughly with conductive particles, and ensure the particles are evenly distributed—because consistency is key. Uneven distribution?
That’s a disaster. We won’t let it happen.
Once mixed, we shape it into sheets or specific gasket forms using compression molding or injection molding.
Then, we apply heat.
High-temperature curing makes the rubber strong and stable, ensuring it can handle real-world applications.
This is serious engineering, folks.
Step 3: Conductive Foil Processing – Precision at Its Best
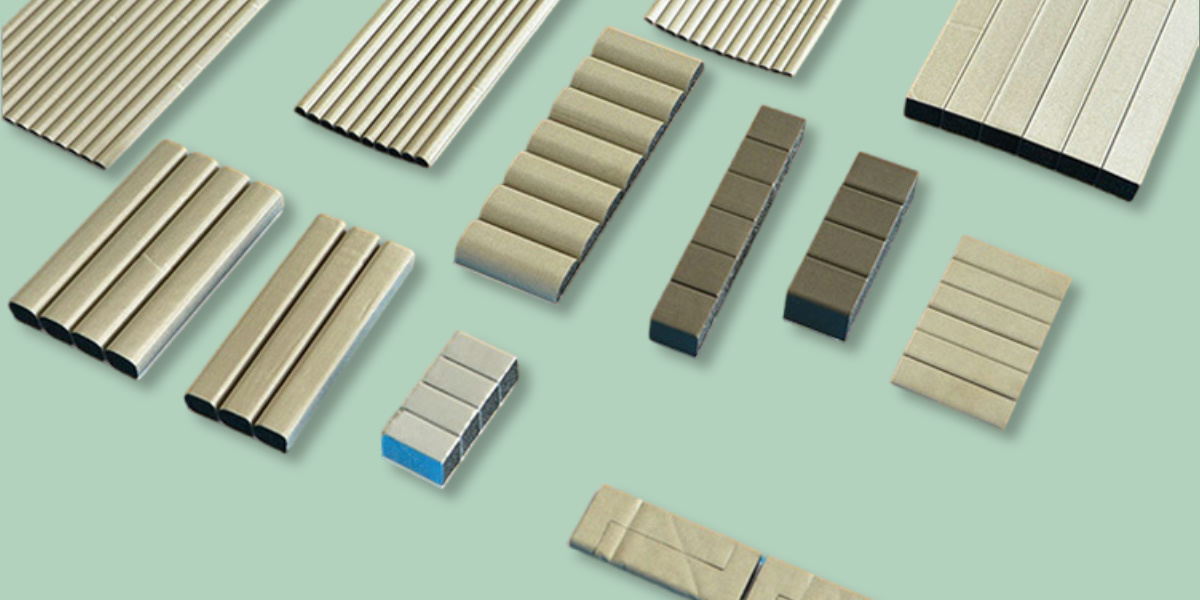
For gaskets that need an extra boost, we use conductive foil.
First, we cut the foil into precise shapes—because precision matters.
Then, we treat the surface to enhance conductivity and adhesion.
This ensures perfect integration with the rubber.
No shortcuts, just quality work.
Step 4: Assembly and Lamination – Bringing It All Together
Now, we combine everything.
If the design calls for it, we laminate conductive foil onto the rubber.
We may use pressure-sensitive adhesive, heat bonding, or other advanced techniques to create a seamless, high-performance shield.
Some designs even require multiple layers—layered rubber, multiple foils, different adhesives—all working together for maximum EMI protection.
It’s all about performance, and we don’t compromise.
Step 5: Precision Die-Cutting – The Perfect Shape
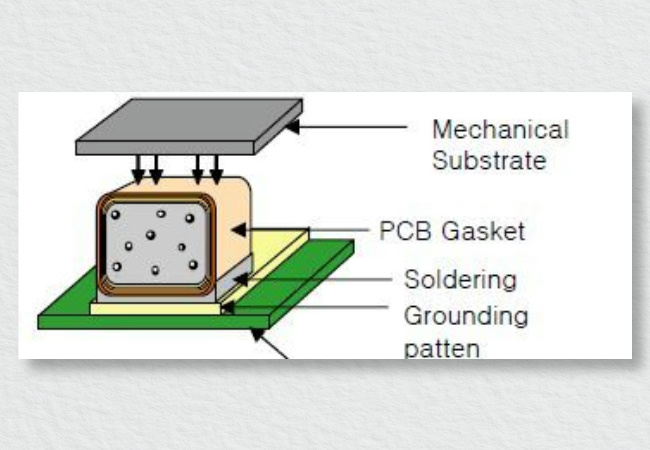
Once the material is ready, it’s time to cut.
And not just any cut—perfect, high-precision die-cutting.
This is where the magic happens.
We use rotary die-cutting, flatbed die-cutting, or laser cutting to shape the gasket exactly as needed.
Tight tolerances, clean edges, zero defects.
For adhesive-backed gaskets, we use kiss-cutting—so the gasket stays on a liner until it’s ready to be used.
Makes installation easy, efficient, smart.
Step 6: Quality Control – Only the Best Pass the Test
Before any gasket leaves the facility, it goes through rigorous testing.
We check conductivity, compression properties, and resilience.
If it doesn’t meet our high standards, it doesn’t ship. Simple as that.
We also test for environmental durability—high heat, freezing cold, humidity, even salt spray.
Because let’s be honest, if a gasket can’t handle real-world conditions, it’s useless.
Step 7: Packaging and Delivery – Safe and Secure
Finally, we clean the finished gaskets, apply a protective film, and pack them in moisture-proof, anti-static packaging.
This ensures they arrive in perfect condition, ready for installation.
Why PCB Shielding Gaskets Matter
Let’s get real. If your electronics aren’t properly shielded, you’ve got problems—big ones. EMI can disrupt signals, cause malfunctions, and even lead to total system failure. That’s not acceptable.
With high-quality shielding gaskets, you get:
Superior EMI protection
Reliable electrical conductivity
Durability in extreme conditions
Precision fit for any application
And the best part? Customization. Need a specific design? Different materials? No problem. These gaskets can be tailored to your exact needs.